Fatigue properties of plastics are not well known, and this lack of knowledge caused an implosion of the plastic viewing dome on the Titan Submarine. Fatigue is a complex failure mechanism in all materials, and the likelihood is questionable that fatigue was adequately investigated before submerging this submarine over and over (Figure 1, "Titan submarine imploded with five people on board", click here"). Most engineers do not well understand this complex fatigue failure mechanism, and the fatigue failure mechanism itself is not well understood.
This article presents a failure analysis of the Titan implosion as this investigation moves forward. Some debris is now available. The Titan was blown apart into many pieces ("Imploded 'Titan' Sub Debris Hauled Ashore After Being Recovered from Ocean Floor: See Photos", click here).
As a matter of fact, a blown-inward viewport theory was opined on June 23rd. This new, June 28th photo further proves this theory, where the plastic viewport, or porthole, is gone. Note that this Op Ed was modified over several days as this story unfolded.
Proof of Theory
As partial proof of theory presented here, Figure 2 shows the recovered front-end of the Titan, where the viewport was blasted inward from its mounting frame ("See Photos of recovered Titan Sub debris after catastrophic implosion during Titanic Voyage", click here).
Figure 3 provides typical fatigue data for steel, which is the most researched material for fatigue cracking. As the number of cycles increases, the stress needed to start a crack decreases. Fatigue was the cause of failure, but the issues surrounding this disastrous failure are far more complicated.
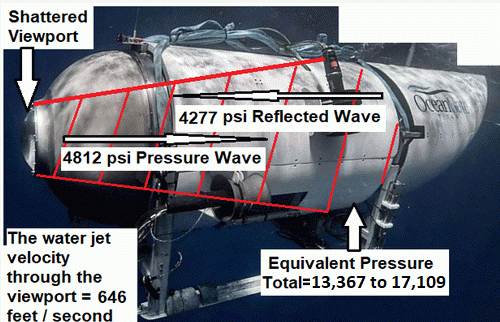
Figure 1. Titan Submarine and pressures during viewport implosion.
(Image by Adapted from Drop The Info / OceanGate by Leishear Engineering, LLC) Details DMCA
The Titan Submarine
This small, 22-feet-long, undersea vehicle dove into the ocean to see the Titanic wreck ("Titanic sub destroyed in 'catastrophic implosion,' all five aboard dead", click here). From photos of the submarine, the weakest link is the plastic portal used to look out on the Titanic.
The "US Navy says it picked up [an] anomaly hours after sub began mission - as it happened" (click here). Interestingly enough, acoustic methods, using sound waves, are available to locate cracks in underground water mains within 50 feet. The sophisticated U.S. Nuclear Navy certainly has technology this good to locate a submarine implosion.
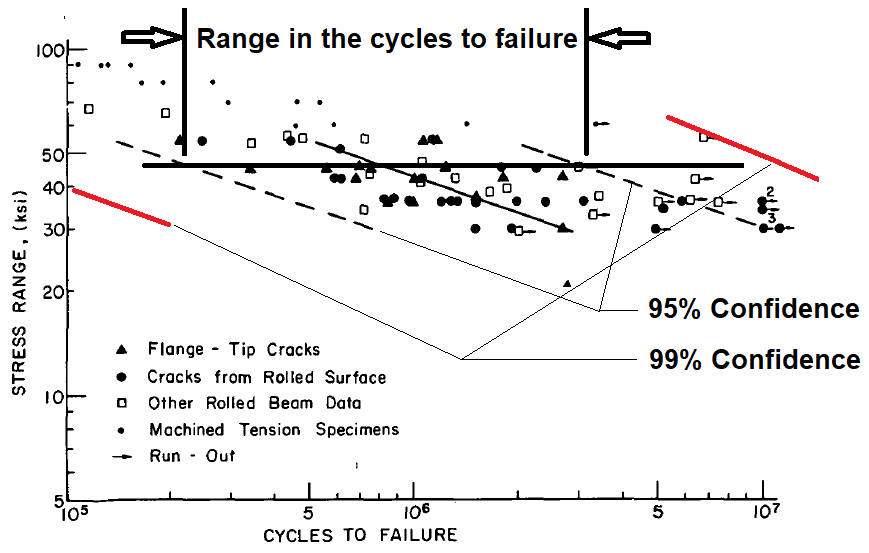
Figure 3. Fatigue properties for steel beams used in highway construction (National Cooperative Highway Research Program Report 147, Fatigue Strength of Steel Beams with Welded Stiffeners And Attachments).
(Image by US government) Details DMCA
Troubleshooting Structural Failures
When troubleshooting a disaster, the type of failure must first be considered. In general, there are three types of failure: overload, creep, and fatigue.
- Overload failures are a one-time failure when a design is grossly incompetent, where a structure fails during first-use. Such a failure did not occur with this vessel, since there were earlier dives to the Titanic.
- Creep causes a material to move when excessive forces or temperatures are applied to a structure. Low temperature creep may have contributed to fatigue failure, but that data may be unavailable for such creep in the viewport materials. Low temperature creep does not occur in metals, but is known to occur in plastics at ambient temperatures. Creep was not an expected failure problem for the carbon fiber hull ("Creep behavior of carbon fiber/epoxy matrix composites", click here).
- Fatigue is certainly the failure cause in this submarine. The only question is which component failed in fatigue. The viewport is the most likely failure candidate, since plastics are the weakest material in the vessel pressure boundary.
As the viewport was pressurized, the viewport was stretched near the center and at the perimeter to induce cyclic stresses in the viewport each time the vessel was submerged or pressurized (Figure 4).
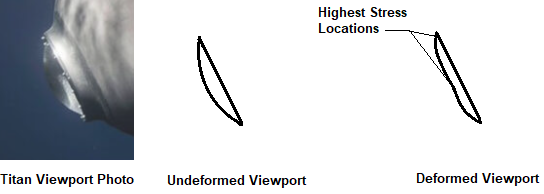
Figure 4. High fatigue stresses on the Titan viewport at the moment of implosion.
(Image by Adapted from Oceangate Expeditions by Leishear Engineering, LLC) Details DMCA
Fatigue Failures
When any material flexes again and again, that material can fail in this process known as fatigue. Cyclic stresses, from repeating applied forces or repeating pressures, create fatigue failures, or cracks. To provide a brief scientific background to explain fatigue cracking, Figure 3 displays experimental fatigue data for steel beams used in bridges.
This figure yields a number of important conclusions about fatigue.
- Hundreds of experiments are needed to predict fatigue cracks.
- Confidence levels of 95% and 99% are shown in the figure.
- 95% confidence level means that this figure is incorrect 1 time out of 20. This confidence level is used for bridge design safety.
- 99% confidence level means that this figure is incorrect 1 time out of 100. This confidence level is used for bridge some nuclear power plant designs.
- For 95% confidence, failures are predicted across a range for the number of cycles that varies by a factor of +/- 10.
- What was the confidence level for the Titan submarine viewport design?
- Extensive experiments have been performed for steels for high-cycle fatigue (thousands to millions of cycles to failure).
- Plastics receive very little experimental testing, as compared to steels.
- Fatigue failures at a low number of cycles are even more complicated, and limited data is available to fully understand low cycle fatigue failures (tens or hundreds of cycles to failure).
- The Titan had only 50 test dives and 3 trips to the Titanic ("How many trips to the Titanic has the OceanGate Titan submersible made and how deep is the wreck?", click here) Therefore, low cycle fatigue is a failure mechanism of the viewport.
A Long History of Fatigue Failures
Fatigue failures hit the presses in the 1960s when two Comet aircraft fell out of the skies in Hawaii. Crashes killed everyone onboard, as the top half of the aircrafts unzipped from those jets. The rivets along the fuselage ripped quickly as each rivet failed in fatigue ("Why Did The de Havilland Comet Jet Airliner Keep Crashing?", click here).
Studies showed that the jets operated safely during routine operations. When these jets aged, they were reassigned to Hawaii for short hops between the islands. However, the repetitive changes in altitude during multiple flights, pressurized the jets over and over. Aluminum jets expand like balloons as they rise into the sky.
Fatigue failures of the jets resulted as the rivets cracked, and the fuselage spit in two different jets.
Fracture Mechanics
During World War II, the Liberty Ships started to crack in two ("Technical Problem Identification for the Failures of the Liberty Ships", .mdpi.com/2078-1547/7/2/20/htm). Investigations in the 1940s re-discovered an earlier theory known as Fracture Mechanics. In 1907, George Irwin's new theory of Fracture Mechanics was dismissed. He cleverly applied calculus and physics to prove how cracks grow bigger and longer. There have been many advances to Irwin's research since the Liberty Ships sunk into the seas, in addition to much experimental validation of theory.
For some cases, once a crack has formed, we can predict how long before the crack rips apart a structure, and we can determine actions to slow down how fast the crack grows. As a mater of fact, the aircraft industry has used fracture mechanics to predict the remaining, safe, operational life of jets and planes.
Fatigue vs. Fracture Mechanics
Some engineers prefer fracture mechanics analysis and some engineers prefer fatigue analysis. Herein lies a problem. Fracture mechanics is based on math and physics, and fatigue theory is based purely on experiments. There is no mathematical correlation between the two theories. As smart as we think that we are, we cannot fully explain fatigue cracks. Experiments are mandatory when structures are subjected to cyclic conditions.
Ongoing Industrial Fatigue Failures
The costs of fatigue failures are astronomical. For example, bridges are cracked all over the U.S. (Figure 5, The U.S. Bridge-Safety Cover-up - Bridge Collapses Kill People).
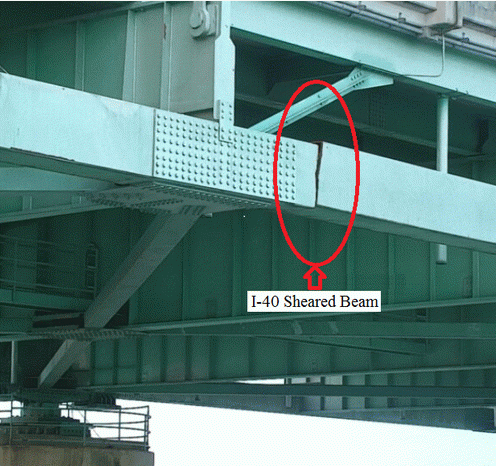
Figure 5. 2022 I-40 bridge damages due to fatigue.
(Image by Arkansas Department of Transportation) Details DMCA
Brand New Fatigue Research
We continue to learn new things about fatigue. This year, an electron microscope investigation proved that millions of microscopic cracks destroy piping systems (Leishear, Figure 6).
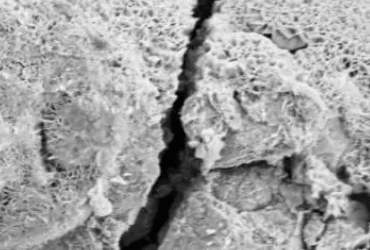
Figure 6. A microscopic fatigue crack in steel piping, magnified 41,000 times (Water hammer and fatigue corrosion -III -An electron microscope study)
(Image by Leishear Engineering, LLC) Details DMCA
The Titan Fatigue Failure?
Failure analysis may not be possible, but fatigue should be carefully considered as money is spent to prove that the Titan design was flawed.
Having spent years performing fatigue failure analysis, I have found that there is very little experimental data available for the use of plastics, such as the plastic used for the Titan viewing portal. The vessel was subjected to many pressure cycles during multiple trips to the ocean floor. I do not have access to specific data, but experience proves that there may have been insufficient experimental data for design.
Even so, fatigue cracks give no warning when they form, and the formation of a fatigue crack in the viewing portal at thousands of psi would almost instantly result in a vessel implosion. The fracture growth rate would have been nearly instantaneous, as water rushed into the vessel at hundreds of feet per second. Shock waves would have been generated into the hull during this violent fluid transient implosion. Once the viewport imploded, the vessel hull would have been damaged, as the hull was destroyed.
An Extremely Complicated Implosion
The complex physics of the Titan implosion may never be fully understood, where even a simplified explanation is complicated. In less than 3/100ths of a second, a high-pressure wave would have doubled inside the hull due to reflected wave effects. The hull would have expanded with an equivalent pressure approaching four to five times the pressure at the depth of the implosion.
Ocean Pressures and Pressures Inside the Titan
Reported in the press, estimated pressures at the depth of the Titanic were 5,500 psi, and the Titan was on the way down to see the wreck. The exact water pressure at the time of the implosion is yet unknown, since the depth of the implosion has not been released by the U.S. Navy. However, assuming that the dive had completed a reported 1-3/4 hours of a 2-hour dive, the pressure can be estimated.
This estimated pressure was 4,812 psi, and the reflected pressure wave inside the cabin would have been 4,277 psi. According to the Leishear Stress Theory, the total equivalent internal pressure on the hull would have approached 13,367 psi to 17,109 psi, where the external pressure was compensated for this calculation ("Fluid Mechanics, Water Hammer, Dynamic Stresses, and Piping Design", R. A. Leishear, 2013, ASME Press, click here). These calculated pressures are shown in Figure 1, where details are not included here. The maximum explosion pressure inside the Titan was 4,812 psi + 4,277 psi = 9,089 psi, where the maximum total pressure pushing outward was 4,277 psi.
Viewport Explosion Scenarios
Assuming that the viewport imploded first, the hull would have momentarily exploded outward, when subjected to such high-pressures. Such a violent explosion would have likely burst the hull.
If the hull had not immediately burst, the hull could have momentarily imploded inward as pressures dropped to the initial cabin pressure for less than 1/100th of a second. Violent cracks or ruptures in the hull would have followed these high-speed pressure changes inside the cabin.
That is, there are three scenarios for the hull destruction: 1) An outward explosion only, 2) An outward explosion followed by an inward implosion, and 3) Multiple cycles of explosion and implosion.
Titan Debris Field
Parts of the sub have reportedly been found on the floor of the ocean at a depth near 12,500 feet, where a remotely operated vehicle 'located two debris fields, a larger one where it discovered the "front end bell of the pressure hull'. 'In a smaller debris field nearby, the robot found the totality of that pressure vessel' ("What's Been Found In The Titan Sub Debris Field So Far", Click Here).
A Viewport Implosion Followed by a Hull Explosion
Given that there were two distinct debris fields, a viewport implosion followed by a single explosion is the demolition cause, where sections of the submarine were blown apart in different directions. For an implosion alone, the sections would be expected to be found closer together ("Submarine ARA San Juan Simulation (Implosion + Sinking) | KRI Nanggala 402 | Titan", .youtube.com/watch?v=QLf_yD-lpF0).
Further Proof of a Viewport Implosion and Hull Explosion
If the hull had imploded, the hull would have crumpled like a paper bag, but it did not. In Figure 7, a section of the hull is shown to have ripped along the seams of the hull and through the body of the hull. Such overload tears in the hull are consistent with a hull explosion, rather than a hull implosion. Note that structural seams, or joints, are typically weak points in a structure, and that a flaw in the hull would have accelerated the rip through the body of the hull.
When the viewport imploded, water rushed in at at 646 feet per second (440 miles per hour). When the inrushing water slammed into a bulkhead inside the cabin, a reflected pressure wave from the bulkhead then further increased cabin pressures to explode the hull.
The hull explosion was caused by this high-pressure reflected pressure wave shown in Figure 1. This second pressure wave in the cabin destroyed the Titan.
Viewport Destruction
In Figure 2, the viewport assembly seems to be entirely removed, even though better photos are need to confirm this statement. Such damage would have occurred if the viewport window was partially imploded. In this case, the reflected pressure wave would have exerted enormous pressures on the window to blast the viewport assembly out into the ocean. That is, high-pressure shock waves from the viewport implosion burst the vessel, and parts of the vessel shot outward as this high-speed explosion evolved, i.e., nearly instantaneous shock waves blew the Titan to pieces.
The Speed of the Implosion and Explosion
This disaster occurred in less than 3/100ths of a second, and the human eye sees 30 to 60 frames per second. At most, the victims saw two frames with their eyes as the water rushed in through the viewport.
An Adequate Failure Investigation?
I am concerned that this investigation will not be adequately performed, since past industrial disaster investigations were flawed with incompetence and lies. "The U.S. Government Murders Us Through Indifference and Deceit - Cover-ups Throughout U.S. Industries".
This article cited flawed investigations and cover-ups of numerous industrial disasters. These disasters included the Fukushima nuclear power plant explosions, the Three Mile Island nuclear power plant explosions, the Piper Alpha oil rig explosion that killed 167 men, and the San Bruno pipeline explosion that killed 8 people.
These major disasters were improperly investigated and information was ignored when that information did not agree with a preferred conclusion. Politicians and engineers alike engaged in major cover-ups for these disasters, for the purpose of protecting those industries from public condemnations. These flawed investigations are the reasons why I am concerned about the future of the Titan investigation.
News Updates
As accident information becomes available, the plausibility of this viewport fatigue theory is validated ("Titanic sub update - Canadian police weigh criminal probe into deaths after vessel implosion", .aol.com/titanic-sub-latest-us-expected-065551188.html). News reports claim that a critical member of the submarine team claims that the hull and viewport were not adequately tested.
Accordingly, the viewport is the failure location, where a fatigue crack in the hull would have imploded the vessel even faster. If the hull imploded, the total equivalent, reflected pressure pushing outward on the viewport could have momentarily equaled up to 4,277 psi. However, an imploding viewport theory is currently endorsed here, where inspections of the debris and autopsies of human remains will provide additional insights.
'In 2018, the company fired David Lochridge, OceanGate's director of marine operations. They claimed he breached his contract and shared confidential information about its designs with two individuals as well as with the Occupational Safety and Health Administration.
However, Mr Lochridge alleged in a wrongful termination suit obtained by The New Republic that he was fired for blowing the whistle about concerning safety issues.
According to the suit, Mr Lochridge delivered highly critical updates regarding the ship's quality control to senior management and OceanGate CEO Stockton Rush, pointing to alleged issues such as 'visible flaws' in the ship's carbon fibre hull, "prevalent flaws" in a scale model, flammable materials onboard, a viewing window not rated for the Titanic's depth, and key safety documents that were not shared with him.
'Now is the time to properly address items that may pose a safety risk to personnel,' he allegedly said at one point. 'Verbal communication of the key items I have addressed in my attached document have been dismissed on several occasions, so I feel now I must make this report so there is an official record in place.'
'He claimed, according to filings obtained by the magazine, that he was fired when he said he wouldn't authorize manned testing of the sub without scans of the craft's hull.' 'The constant pressure cycling weakens existing flaws resulting in large tears of the carbon. Non-destructive testing was critical to detect such potentially existing flaws in order to ensure a solid and safe product for the safety of the passengers and crew.'
Note that this fired 'director of marine operations at the time was 'responsible for the safety of all crew and clients', and he wanted more non-destructive testing. However, he did not demand more fatigue testing. He overlooked the probability of a fatigue failure. As I stated, most engineers do not clearly understand fatigue cracks and resulting ruptures, and this complainant was a submersible pilot rather than an engineer. Misunderstandings of fatigue cracks can be dangerous.
Human Remains
"Human remains thought to be found in Titan sub debris" (https://www.bbc.com/news/world-us-canada-66049789). If bones are recovered from human bodies, then there is a reasonable probability that plastic shards from the viewport may be imbedded in those bones. Failure analysis is the process of gradually understanding complex phenomena.
The Price for New Technology
New technology in hostile environments is dangerous. For example, the U.S. space program was successful, but the X-15 program preceded the space program, and crashes blasted from the air into the ground as new technology advanced (Figure 8, "X-15 Photo Collection", .dfrc.nasa.gov/Gallery/Photo/X-15/HTML/E-9149.html.
Schedules and Expenses Become More Important Than Science and Safety
Managers are one of the greatest problems to the advance and application of science. With a successful space program in place, two space shuttles crashed and killed the crew. In both cases, there were technical concerns that were raised during design. In both cases, the safety concerns were dismissed by management, and the spacecraft exploded (Figure 9, "What NASA Could've Done Differently To Prevent The Space Shuttle Challenger Explosion In 1986:, click here).
There are claims that the same mindset was executed in this submarine implosion ("Titan tragedy: Canada launches investigation; CEO of sub company 'dismissed safety fears' - as it happened", click here).
Objective Dangers
At the risk of sounding callous. 'Objective Dangers' are known in all dangerous endeavors.
I have jumped a motorcycle ten feet off of the ground at 95 miles per hour; climbed mountains; climbed rock faces; climbed walls of ice; rafted Class V white water; canoed white water alone for days; scuba dove; snorkeled with small sharks, barracuda, and dangerous bull sea lions; jumped out of airplanes with a parachute; snow skied - alone - into the White Mountains of New Hampshire in sub-zero Fahrenheit temperatures; and hiked across mountain tops in 120 mile per hour winds and rain in winter.
Fortunately, my only injuries were a few small cuts; abrasions; minor frostbite; a bloody nose from rising too fast from a scuba dive when my weights fell off as I shot to the surface; and a dislocated finger when I opened my parachute too early. When my chute opened early, I dropped 20 feet to the ground to land on my pinky finger. Half of my pinky finger then formed a right angle with the rest of my finger, so I popped it back into place, and there was only a minor bone chip.
Obviously, there are dangers in dangerous adventures. Even so, for all of these activities, I either undertook the dangers on my own, or I signed a waiver that there was risk of injury and death.
We Accept the Risks for the Adventures
None of us believe that we will be injured or die when we sign, but we sign for the adventure anyway. We give our word that we understand the risks, and in return we experience risks and adventures that most people decline and never get to experience.
Reportedly, the adventurers on the Titan signed a similar waiver.
'But before boarding submarines from OceanGate, travelers were warned in a contract that it has not been approved or certified by any regulatory body, and could result in physical injury, disability, motion trauma, or death'.
Courts and legal agencies will decide civil and criminal liabilities.
Even so, science is paramount in the investigation of the Titan implosion.
Addendum
Along with a link to this Op Ed, the following email was sent to the Canadian Mounted Police and to the U.S. Coast Guard. These organizations are involved with investigations of the Titan implosion.
The Titan submarine was a tragic disaster, but I believe that I can add insights to aid this ongoing investigation. I am not a submariner, but I am a failure analysis expert.
Accordingly, I have published an Op Ed, titled, "The Titan Submarine Implosion - A Fatigue Crack Ruptured the Viewport to Instantly Destroy the Vessel". The information that I published was evident to me as soon as I heard about this disaster.
Perhaps a common goal should be to learn and prevent future disasters, rather than establish blame. In this light, perhaps my insights will be helpful.
(Article changed on Jul 02, 2023 at 5:47 PM EDT)