Fatigue crack failures are prompted by repetitive loads, or vibrations, over and over. Helicopters are massive vibration machines. Therefore, fatigue was a probable cause for this Hudson River helicopter crash.
The Crash
In a terrible accident, a helicopter broke into pieces, the helicopter dove into the Hudson River upside down, and all passengers were killed. Some people are claiming that helicopters are safe since so few people are killed, i.e., 37 people have died in New York helicopter crashes since 1977 (Figure 1, "What went wrong before helicopter crashed into Hudson River", .youtube.com/watch?v=cSbDjcNlrok). Earlier on April 11, 2025, claims were made that helicopters are safe in spite of this accident. If we do not know the cause, how can we claim that safety is protected?
Later on 4/14/2025, the affected helicopter tour company shut down, the Federal Aviation Administration grounded helicopters from that company, and safety was no longer stated to be protected, since people drowned on an earlier tour with this company ("FAA says helicopter company in deadly Hudson River crash is shutting down", click here). When this article was written, a request to the Federal Aviation Administration was included to consider grounding the helicopters of the same design. The FAA will consider helicopter safety in a meeting on April 22, 2025. Given this new information, such a request is no longer required.
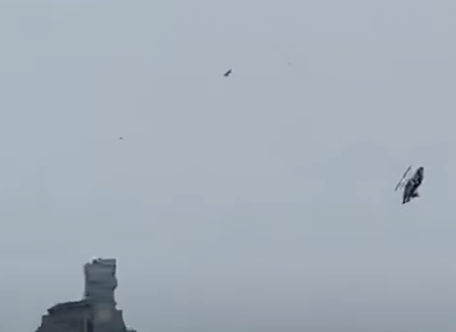
Figure 1. Hudson helicopter crash, 4/10/2025.
(Image by News (abcnews.go.com/Site/fullpage/abc-news-terms-conditions-license-agreement-14225050)) Details DMCA
NTSB Investigation
The NTSB (National Transportation Safety Board) will investigate this crash in competent detail. If fatigue cracking was a possible problem, more crashes are possible. Since this crash has not yet been evaluated, let's look at fatigue cracks in other industries and the applicable theory to explain such cracks.
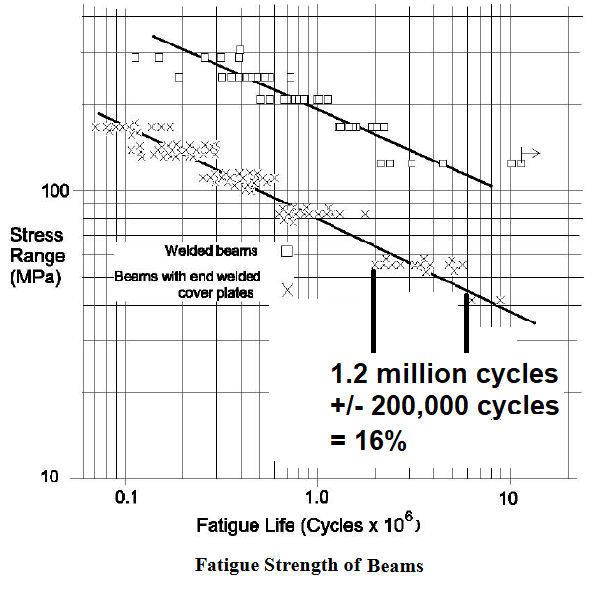
Figure 2. Bridge fatigue data shown, where fatigue crack failure data may vary due to size and shape of the structure or machine.
(Image by Department of Transportation, 'Steel Bridge Design Handbook: Design for Fatigue') Details DMCA
Fatigue Theory and Fracture Mechanics Theory
Fatigue theory proves that cracks are directly related to the magnitude of an applied vibration and the number of cycles to failure. That is, the more that a structure or machine is bent back and forth the more likely that structure is to crack, and the greater the applied force for that cyclic load, the more likely the structure will crack. More cycles or more force accelerate failure.
Fatigue theory is far more complicated. Fatigue cracks start at microscopic defects that are inherent in all materials, and therefore structures of the same design crack at different times. In fact, the cracks form due to cycles to failure over a range of plus or minus approximately 16%, or more, cycles for some structures, which means that if the first cracks start 20 years after one structure is first built, half of the identical structures will fail in 23.2 years after they are built (bridges in this example). Another important fact about fatigue is the concept of a fatigue limit, where this concept claimed that there was a number of cycles beyond which fatigue cracks could not form. These statements are based on data for bridges, which may vary for the number of cycles to failure for helicopters, which is unavailable to date (Figure 2). Even so, the principles are the same; if helicopters initially fail in fatigue, more failures will follow.
Also, the American Society of Mechanical Engineers has shown that fatigue cracks will start beyond this so-called fatigue limit (ASME B31.3). Accordingly, some engineers who have not kept up with these new developments still believe that once the fatigue limit has been reached a structure cannot fail, which of course is incorrect.
Additionally, a little known and little investigated aspect of fatigue is that metals get harder when fatigue cracks form. In fact, I used a hardness tester in the 1990s to show that the steel surrounding a fatigue crack on a pressure vessel was harder than the steel on the rest of that vessel.
In other words, hardness testing may be a means to inspect for fatigue cracks before they form. This method could be added to the available methods for crack detection that are used in aircraft today, i.e., visual dye penetrant, eddy current and sonic testing.
Fracture mechanics theory proves that once a crack has formed in a structure, the rate of crack growth can be predicted. That is, if a crack is found on a structure subjected to cyclic stresses, the time for that crack to rip apart that structure can be predicted.
Fracture Mechanics Theory in Use
Let's look at the application of fracture mechanics theory. Although fracture mechanics theory was invented in the early 1900s, it's first major uses were to investigate the breakups of Liberty ships in World War II and investigate the crashes of Comet jets in the 1950s. The investigation of the Comets advanced this theory significantly.
Two different Comet jets crashed before the Comet fleet was grounded for investigation. With frequent flights, the jets were subjected to frequent expansions of the fuselage, or jet body, which in turn increased the forces on the fuselage. That is, when jets reach altitude, the pressure inside the cabin expands the fuselage slightly as if it was an aluminum balloon. The fuselage expansion caused fatigue cracks. When the cracks grew large enough, the cracks tore apart the jets and the jets crashed. An important finding of this accident was that two jets crashed, killing all passengers and crew, before these jets were grounded, since the first crash was considered to be an anomaly.
'Sadly, the Comet, even after the cause of its mystery woes was diagnosed, had a terrible safety record, with 26 hull losses during its short operational life, resulting in more than 400 fatalities (Figure 3, "Why Did The de Havilland Comet Jet Airliner Keep Crashing", click here)'.
Fracture mechanics theory is in widespread use today. As an example, this theory has been used to evaluate cracks on in-service aircraft to allow jets to fly when cracks are too short to grow by themselves. Yes, jets have been allowed to fly with known cracks, based on competent engineering theory. Fracture mechanics is used in many industries to assess actions required during service when cracks are identified ("ASME FFS1, Fitness for Service" for piping and pressurized equipment). I have personally used ASME-FFS1 to permit cracked piping to remain in service in nuclear facilities, once the cause of the cracks was reduced to a safe level.
Fatigue, Fracture Mechanics, and Helicopters
In short, fatigue theory predicts when small cracks will start, and fracture mechanics predicts if those cracks will grow into major cracks that can be catastrophic. Together these theories are used to improve initial designs and troubleshoot in-service failures.
An important implication of the facts about fatigue and fracture mechanics theory is that cracks will eventually form in helicopter components. An important question is how many years before cracks are first seen, and whether, or not, those cracks are dangerous. This question overshadows any ongoing investigation of this crash.
A Safety Question
When cracks form in structures or machines after initially being placed in service, the typical failure mechanism is fatigue. There were obviously cracks in the helicopter, and fatigue failure is a probable cause of cracks. Since the affected helicopter tour shut down, the question becomes, 'are there other similarly affected helicopters in service, and should those helicopters be grounded?' 'The [FAA] said it is analyzing airplane and helicopter hotspots nationwide and will be hosting a helicopter safety panel on April 22 to discuss the findings, risks and additional mitigation options.'
Addendum, 4/15/2025
The following email was sent to the FAA.
I suspect that fatigue failure will be considered during this FAA crash investigation. I have expressed this opinion in an Op Ed, titled, "The Hudson River helicopter crash and future crash dangers from fatigue crack failures?". A partial grounding of helicopters seemed warranted, but perhaps the response should be widened to other helicopters.
Thank you.
Robert A. Leishear, PhD, PE, PMP
ASME Fellow
Doctor of Mechanical Engineering, U of S Carolina (Water Hammer and Explosion Failure Analysis)
Master of Engineering in Nuclear Engineering, U. of S. Carolina (Explosions in Piping and Nuclear Reactor Systems)
Master of Science in Mechanical Engineering, U of S Carolina (Fluid and Piping System Failure Analysis)
Expert in Numerical Analysis with Ansys, Technological University of Madrid
Bachelor of Science in Mechanical Engineering, Johns Hopkins University
Combustion Institute, Princeton University
Nuclear Reactor Design, Oak Ridge National Laboratory
International Radiological Protection, NEA, U. of Stockholm
International Nuclear Law, NEA, U. of Singapore
NACE Senior Corrosion Technologist
NACE Senior Internal (Piping) Corrosion Technologist
NACE Cathodic Protection Tester
AMPP Certified Coatings Inspector
NACE Corrosion Under Insulation
Shift Technical Engineer
Metrologist / instrumentation Engineer
Structural Steel Fitter and Welder
Instrumentation / HVAC / Electronics Technician
Journeyman Sheet Metal Mechanic
Who's Who in America, Top Engineers
Mensa, Copper Black Award for Creative Achievement
Leishear Engineering, LLC
Engineering Consulting and Research
205 Longleaf Court, Aiken, SC, 29803
Website - leishearengineeringllc.com
803-641-6753
(Article changed on Apr 15, 2025 at 4:35 PM EDT)